Development of Regenerated Bacterial Cellulose Fibres from Sustainable Source
Cellulose is the most abundant organic polymer found in nature. It can be
widely found in plants, or can be produced by bacteria. Cotton and wood
are two common cellulose-rich raw materials which are used to produce
regenerated cellulose fibres for textile applications.
However, cotton farming requires substantial amounts of pesticides and
water, while the production of wood-based regenerated cellulose fibres,
such as viscose fibres, also involves the use of environmentally harmful
chemicals like hydrogen sulphide (H2S) or carbon disulphide
(CS2). Addressing these issues, The Hong Kong Research
Institute of Textiles and Apparel (HKRITA) has utilised the bacterial
cellulose (BC) derived from the fermentation of kombucha and developed a
new solvent system to produce regenerated cellulose fibres.
Turning Food Waste into Useful Textile Fibres to Mitigate Environmental
Impact
Kombucha tea is a fermented sweetened black tea produced by a symbiotic
culture of bacteria and yeast (SCOBY). The SCOBY waste, a gelatinous BC
pellicle, is usually disposed of after beverage production. In this
project, this pellicle is collected and recycled as the raw material to
produce regenerated cellulose fibres.
The production processes involve purification, drying, grinding,
dissolution, and spinning. First, the BC pellicle is completely immerged
in a specially prepared aqueous solution to remove the unwanted residual
medium and other impurities. The clean and white film is then dried by
vacuum oven heating or freeze drying. The dried cellulose is shredded into
small pieces and ground into fine powder for making a solution. Finally,
the cellulose powder is dissolved in the new solvent system to produce a
cellulose dope for spinning. Using conventional wet spinning methods, the
solution is then spun into BC fibres.
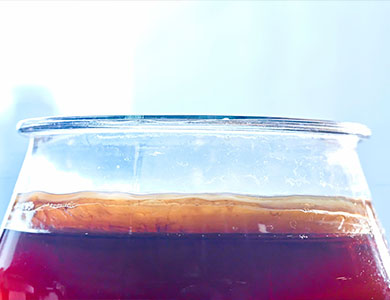
The gelatinous BC pellicle produced during the fermentation of
kombucha
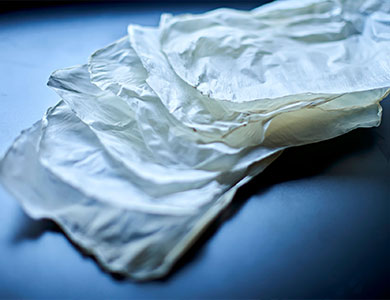
Dried BC pellicle
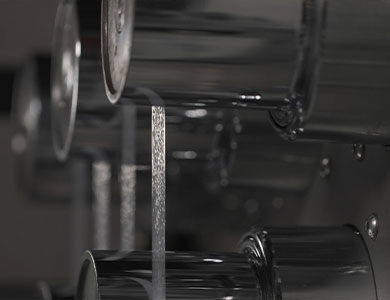
Producing BC fibres using wet spinning process
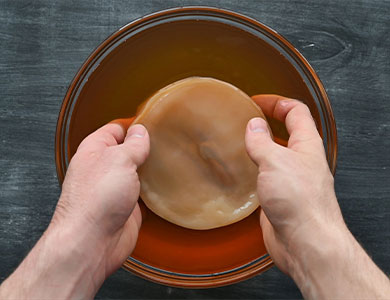
Project video
The process of making regenerated BC fibres is more environmentally
friendly than plant-based cellulose fibres production. In comparison to
cotton, it takes only 10 to 14 days to ferment BC whereas cotton growth
takes 150-180 days. Its water consumption is less than that of cotton
farming, and it is pesticide-free. Comparing to viscose fibres, the
production of BC fibres avoids deforestation and the use of
environmentally harmful chemicals.
Furthermore, the project has made a successful attempt to replace refined
sugar with sugar from discarded melon peels during the production of
kombucha.
A New Solvent System that Overcomes Material Constraints
BC has high degrees of purity, polymerisation and crystallinity, and is
thus a promising alternative for cellulose fibre production. However,
these features also limit its application in the solvents and production
systems available in the market. This project overcomes the challenges of
a high degree of polymerisation and crystallinity by developing a novel
aqueous solvent that does not involve toxic chemicals. This solvent can
dissolve BC with high polymerisation levels at room temperature, reducing
additional energy consumption that is needed for heating. Moreover, the
solvent is 98% reusable, making the entire production process even more
environmentally friendly.
This regenerated BC fibres have passed tests for fibre strength and
elasticity, achieving a tensile strength comparable to viscose fibres. The
research team has also successfully created dyed fibres, yarns, and sample
garments. If mass-produced, these regenerated BC fibres would offer a more
sustainable choice of textile material for the fashion industry.
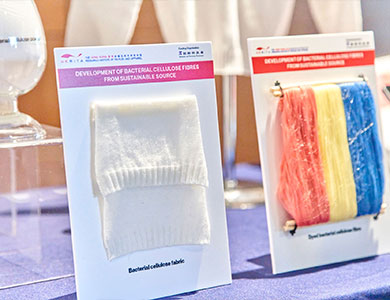
Dyed fibres and fabrics made from the regenerated BC fibres
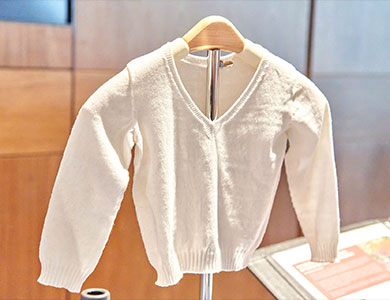
The sample garment has a soft hand feel and elastic texture